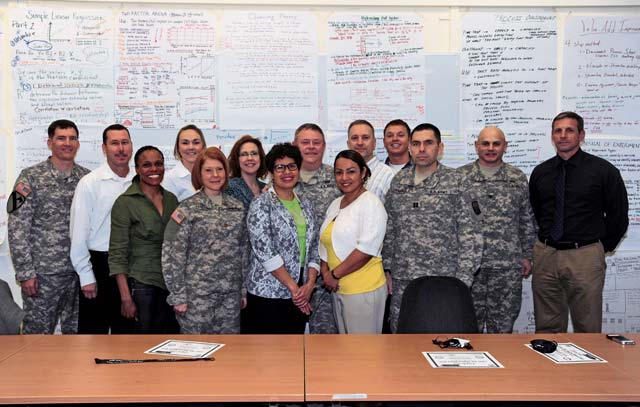
The 21st Theater Sustainment Command formally recognized a graduating class of 12 newly trained Lean Six Sigma black belts during a ceremony April 18 on Panzer Kaserne.
The new black belts, nine of which are from the 21st TSC, will be responsible for implementing improvement projects within their organizations in order to increase customer satisfaction levels, productivity and to save money.
Throughout the course, the students “learned the full (problem-solving methodology),” said Maj. Chris Bachmann, the 21st TSC chief, Operations Research System Analysis section. “They learned a suite of tools that allows them to look at problems that fit the LSS methodology in order to improve processes within their organizations.”
Thomas Axtman, the deputy chief of current operations for the 21st TSC, said he learned quite a bit.
“I learned that there is a scientific way to validate what we may or not know by experience is in fact the correct answer. Now I have the calculations, the equations, and the process to scientifically validate what is correct,” he said.
Bachmann agreed and said the class was very interesting. “They asked questions, they were interested in what they were learning, and they were able to have a good time,” he said.
Having the ability to enjoy learning was an important part of the process, Bachmann said.
“When you’re digesting as much information as we teach in the class, and if you’re not having fun at the
same time, it gets very tough,” he said.
During the four-week course, which was spread out over four months, the newly graduated black belt professionals learned valuable techniques and lessons which they can now take to their organizations to help save money and increase productivity.
“LSS is a great process-management tool that fosters a culture of continuous improvement with a holistic process and methodology that maximizes collective solutions and value by achieving improvements in cost, quality, process speed, and resource utilization. This process is especially important, given our current fiscally constrained environment,” said Col. Barry Diehl, the chief of staff for the 21st TSC.
“This is the first performance improvement initiative that I’ve seen that really makes a difference and really has an impact,” Axtman said. “Now my long-term goal is to assist the 21st TSC and the Army by taking on these challenges and helping them to be more efficient and less wasteful in a way that makes more sense.”
The graduates represent the first ever black belt certification course which was organized and sponsored by the 21st TSC.
“For the short term at least, the 21st TSC is going to be the hub of LSS training within the (U.S. Army Europe) footprint,” Bachmann said. “This class had folks not only from the 21st TSC, but we also had folks from (Installation Management Command-Europe), we had folks from NATO, and we had folks from USAREUR.”
Bachmann added that the next class will have the same diversity.
“Not only will we have a lot of the staff sections from the 21st represented, but we will also have four individuals from different organizations within USAREUR and two from the Air Force that have signed up,” he said.
Bachmann said he believes it’s not good enough for organizations to just send their service members and employees to the training; they must also see the value in LSS and make its incorporation a priority for the organization.