Story and photo by Tech. Sgt. James M. Hodgman
U.S. Air Forces in Europe and Air Forces Africa Public Affairs
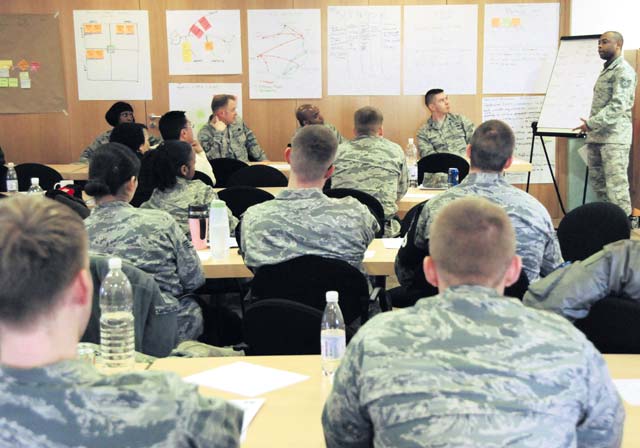
Airmen first class to colonels and civilians from more than 10 Air Force specialties discussed ways to improve work center processes and remove waste during the Air Force Smart Operations for the 21st Century Continuous Process Improvement Course here April 1 to 4.
The four-day class, also referred to as the Green Belt Process Improvement Course, consisted of 55 students, the largest CPI course in Air Force history.
Janet Boyd, a senior CPI analyst with the U.S. Air Forces in Europe and Air Forces Africa Business Transformation Office and the lead instructor for the class, said she’s proud of how the BTO team came together to support the class.
“We are used to working in smaller classes so everyone in the BTO had to put our heads together, because there were a lot of logistics involved in this,” Boyd said. “Everyone applied their input. I had a lot of help from the BTO team and the class wouldn’t have been possible without everyone on the team contributing; that’s why this was successful.
“I was a little nervous about the class because the class was so large and it had never been attempted before,” she added. “I was proud to be a part of it.”
The CPI course is designed to teach people how to identify and eliminate non-value added activities within processes.
Staff Sgt. Bronshay M. Limson, a quality assurance inspector for the 86th Medical Operations Squadron, said he enjoyed the CPI course and has already started applying process improvement tools in his office.
“The tools I learned in the CPI class will give me the opportunity to analyze our current processes and ask the questions,” Limson said. “Is there any value to the way we conduct business now and where is the waste that can be trimmed?
“I have already started and my co-workers are on board with some of the improvements,” he continued. “For example, my job requires a lot of walking and at the end of the night a detailed brief is provided to the production supervisor about all QA (quality assurance) inspections done that day.”
Much of this walking Limson describes requires Airmen to leave their work areas to reference Air Force Instructions. This reduces the time Airmen have to perform their specific mission.
“I made the suggestion of installing commonly used AFIs on our e-tools to cut down on the time needed to walk back to the office and look up the reference,” Limson said. “This improvement not only gives time back to inspectors, but also gives leadership a much needed head start in case a root cause analyst report must be accomplished.”
Before attending the CPI course, students were asked to review processes in their units and identify a task that could be performed more efficiently. The students then used the eight step problem solving model, along with other tools, to find ways to enhance that particular inefficiency. Students also worked to develop solutions in small groups.
The class tackled some important topics including the officer performance report process, assigning people to the appropriate Air Expeditionary Force band and scheduling squadron leave.
Capt. Stuart G. Jessup, an operations flight commander with the 86th Communications Squadron, was a member of the group that tried to develop a solution to the AEF assignment process. He said the class was a valuable experience.
“Every person assigned to USAFE is assigned to an AEF band; however, we’re not currently at 100 percent. We worked on ways to tighten up the process to bring the command into compliance,” Jessup said.
While working a deployment issue doesn’t sound like something that falls in the communications specialty arena, Jessup said the way the CPI course teaches students to analyze problems provided a foundation to analyze processes in his unit.
“Even though we were working a problem that didn’t relate to the communications squadron specifically, the analysis tools can still be applied to the communications squadron and are applicable to IT type questions as well,” he said.
“One thing I took away is not rushing to jump to a conclusion,” Jessup added. “The eight step problem solving model forces you to break down the problem before you start running toward a solution to make sure you’re running in the right direction.”
A major focus area of the CPI class is finding ways to enhance processes thereby making those processes more efficient, something everyone can benefit from, said Thomas L. Jones, a process improvement and business strategy analyst with the USAFE-AFAFRICA BTO.
“Especially with the environment we’re operating in today with the budget and resource constraints we have, it’s even more important that everyone is engaged and keeps an eye toward improvements in their areas,” Jones said.
The command completed 26 AFSO 21 projects in 2012, which led to more than $6 million in savings and a reduction in man-hours of 90,000, according to the USAFE-AFAFRICA BTO.
The CPI course is open to all Airmen and civilians assigned to the USAFE-AFAFRICA theater. Currently, the course is offered here and at Royal Air Force Lakenheath and Mildenhall in the United Kingdom.
For more information about future CPI courses, email the USAFE-AFAFRICA BTO at usafebto.bto@us.af.mil.