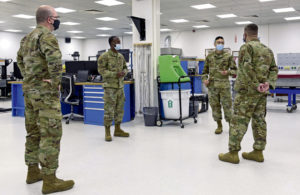
Using the 86th Airlift Wing’s line of effort of Develop Airmen and Care for Families as a guideline, 86th Maintenance Group leadership created a new mentorship program.
The objective of the new program, MxMADE, is to provide a foundation for maintenance members to leverage their intellect and thirst for improvement to develop Airmen who can improve mission capability and success.
“MxMADE stands for Mentor, Adapt, Deliver, and Empower and is aimed at improving not just the members themselves, but those around them,” explained Col. Anthony Nance, 86th MXG commander.
Leadership developed the program after taking feedback from officers, enlisted and civilian personnel from various ranks and career fields in the group’s organization about what they identified as needs and priorities surrounding mission and training.
“It was conceived with input from our entire organization. It wasn’t just leaders coming together in a bubble and concocting this,” said Chief Master Sgt. Alan Malcolm, 86th MXG superintendent. “We’re accountable to the Airmen and we owe it to them to develop them.”
Airmen also share their successes of the program, delivered through multiple avenues including shadow programs and academics, and how the strategy keeps maintainers focused on what is important during weekly staff meetings and impromptu interactions during day-to-day operations.
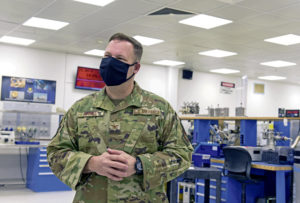
“Empowerment is an element that gives us motivation and drive,” said Senior Airman Angelo-Miguel Lopez, 86th Maintenance Squadron precision measurement equipment laboratory technician. “It provides a sense of ownership and investment in our work because without it, we would treat our mission like a regular nine to five job.”
Dialogues often spark innovation and modernization discussions on how to complete the mission more efficiently.
One innovative idea involved equipment calibrations and COVID-19 travel restrictions.
“Normally, we would send people to various locations in Europe to calibrate equipment too large to be shipped, such as aircraft scales and fabrication ovens,” said Lopez. “Due to COVID-19 travel restrictions, we weren’t able to do those calibrations as normal; but our customers still need their items calibrated to accomplish their mission.”
Lopez explained that with leadership empowering them to put their heads together, the Ramstein PMEL laboratory has become the first to do “virtual calibrations,” ensuring missions continue all over Europe.
“To transition a good team to a great team, you have to have buy-in from the team,” said Nance. “Every member has to know they are a valued member of the team; their input matters and they are empowered to not just make those around them better but the entire organization better. From the smallest idea to the largest that we can put into action that helps the organization.”
