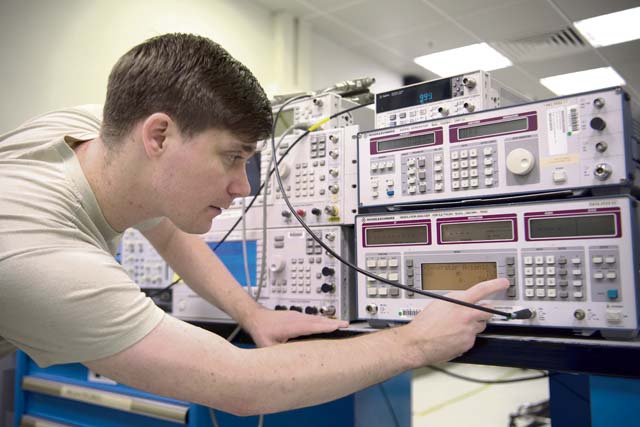
Most tools are designed to do one thing and to do that one thing perfectly. From flight systems in an aircraft measuring altitude, to the scales used to measure the weight of a vehicle, everything is calibrated to perform its function perfectly. When those items start to fail, the mission is affected and something needs to be done about it.
That’s where the 86th Maintenance Squadron’s test measurement diagnostic equipment flight, better known as PMEL, comes into play. These Airmen bring tools and items back to their factory specifications to ensure the mission is completed properly and according to specification.
The mission of the PMEL flight is to ensure safe, accurate, reliable, and traceable measurement equipment to the warfighter.
The PMEL flight at Ramstein is one of a limited number of locations in the Air Force. Due to the environmental requirements set by the Air Force Metrology and Calibration Program, items are sent from installations from all over U.S. European Command, U.S. Africa Command, U.S. Central Command, and U.S. Transportation Command, for calibration.
“The PMEL flight supports and maintains an inventory of over 14,000 tools and measurement items,” said Master Sgt. David Valdez, 86th MXS laboratory section chief.
Airmen who train as PMEL technicians undergo an eight month technical training school before they get to their first base. Once at their first base, they continue to train.
“The biggest challenge is getting the newest Airmen trained to a point where they are proficient enough to perform the mission without continued oversight,” said Valdez. “This usually takes anywhere from eight to 12 months.”
Calibrations are accomplished by Airmen trained in sections specializing in different functionalities.
The K1/K8 sections calibrate electrical items that deal with voltage, resistance, current, and capacitance. Some of the items include counter measure tests which test the flare systems on the C-130J Super Hercules.
The K3/K4 sections calibrate items that deal with time, frequency, power, and waveform analysis. These items can include tactical air navigation systems both onboard the aircraft and on the ground.
The bulk of the work done by the PMEL flight is calibrating test equipment that falls under the K5/K6 section, which are items that deal with force, torque, pressure, temperature, along with some specialty items. These items can include torque wrenches used by maintainers, to scales used by the Office of Special Investigations.
“It is paramount that my job be performed correctly, as the measurement tools I certify are trusted by Airmen out on the flight line,” said Senior Airman Wayne Meacham, 86th MXS PMEL journeyman.
On top of performing calibrations on tools and measurement items, Airmen are also required to determine the faults of a broken item, before sending the item back to the owning squadron.
“The work the flight performs has far reaching impacts,” said Chief Master Sgt. Donald Ledbetter, 86th MXS TMDE flight chief. “As a pilot glides into a landing, they need to know their altitude. They have an altimeter in the cockpit, but how do they know the altimeter is correct? They know because a crew chief has checked it. How does the crew chief know their equipment functions correctly? Because they brought it to our flight.”
With a rotating inventory of more than 14,000 items, PMEL technicians keep themselves busy, and Europe stays calibrated.